หลักสูตรพัฒนาบุคลากรด้านการผลิตชิ้นส่วนยานยนต์ไฟฟ้า (หลักสูตร Non-Degree)
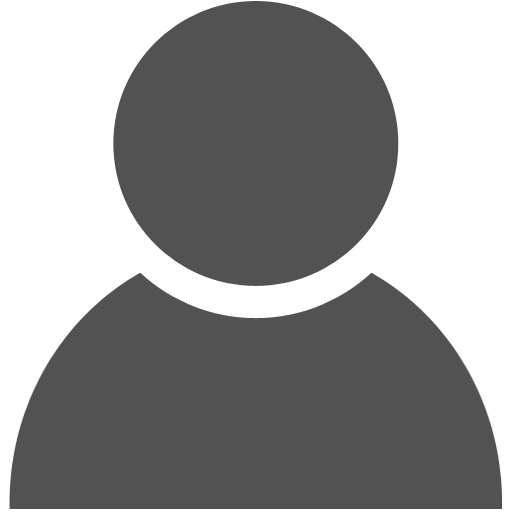
การนำหลักการลีน (Lean) มาใช้ในการผลิตชิ้นส่วนยานยนต์ไฟฟ้าเริ่มต้นด้วยการกำจัดความสูญเปล่า (Waste) ทุกประเภทในกระบวนการผลิต ซึ่งรวมถึงการลดเวลารอคอย การลดการเคลื่อนไหวที่ไม่จำเป็น และการลดปริมาณของเสีย จากนั้นใช้เทคนิค 5S เพื่อสร้างสภาพแวดล้อมการทำงานที่เป็นระเบียบ สะอาด และปลอดภัย โดยมีการจัดระเบียบพื้นที่ทำงาน (Sort), จัดเก็บอุปกรณ์อย่างเหมาะสม (Set in order), ทำความสะอาดพื้นที่ (Shine), กำหนดมาตรฐานการทำงาน (Standardize), และรักษาวินัยในการทำงาน (Sustain) ต่อมาจะมีการนำหลักการปรับปรุงอย่างต่อเนื่อง (Kaizen) มาใช้ ซึ่งเป็นกระบวนการที่ทีมงานร่วมกันระดมสมองเพื่อหาวิธีการปรับปรุงกระบวนการผลิตอย่างต่อเนื่อง นอกจากนี้ยังมีการใช้การวิเคราะห์กระบวนการผลิต (Value Stream Mapping) เพื่อระบุและวิเคราะห์ขั้นตอนที่สร้างมูลค่าและขั้นตอนที่ไม่สร้างมูลค่า เพื่อให้สามารถปรับปรุงและกำจัดขั้นตอนที่ไม่จำเป็นได้ ผลลัพธ์คือการลดต้นทุนการผลิต เพิ่มประสิทธิภาพในการทำงาน และเพิ่มมูลค่าในกระบวนการผลิต ทำให้การผลิตชิ้นส่วนยานยนต์ไฟฟ้ามีประสิทธิภาพและคุณภาพสูงขึ้น
ผลผลิตที่เกิดจากการนำหลักการลีนมาใช้ในการผลิตชิ้นส่วนยานยนต์ไฟฟ้าคือการผลิตที่มีประสิทธิภาพสูงขึ้น โดยสามารถลดเวลารอคอย ลดการเคลื่อนไหวที่ไม่จำเป็น และลดปริมาณของเสียได้อย่างมีนัยสำคัญ การใช้เทคนิค 5S ทำให้สภาพแวดล้อมการทำงานเป็นระเบียบและปลอดภัย ซึ่งช่วยเพิ่มประสิทธิภาพในการทำงานของพนักงาน การนำหลักการ Kaizen มาใช้ทำให้เกิดการปรับปรุงกระบวนการอย่างต่อเนื่อง และการใช้ Value Stream Mapping ช่วยระบุและกำจัดขั้นตอนที่ไม่สร้างมูลค่า ผลลัพธ์ที่ได้คือการลดต้นทุนการผลิต เพิ่มประสิทธิภาพในการทำงาน และเพิ่มมูลค่าในกระบวนการผลิต ทำให้การผลิตชิ้นส่วนยานยนต์ไฟฟ้ามีคุณภาพสูงขึ้นและสามารถตอบสนองความต้องการของตลาดได้อย่างมีประสิทธิภาพ